Mold Cleaning
The mold cleaning process will be carried out after each demoulding process. Cleaning the abrasive tool is to remove impurities attached to the surface of the abrasive tool. This helps maintain glove quality and yield. AIBON uses multiple cleaning procedures. First, use clean water to wash away the remaining impurities on the surface. Then use a brush to clean the abrasive tool 360 degrees. This will completely wash away the surface substances. Then filter it with clean water to thoroughly clean the abrasive tool, easy to operate, high efficiency and no dirt will enter the inside of the gloves.
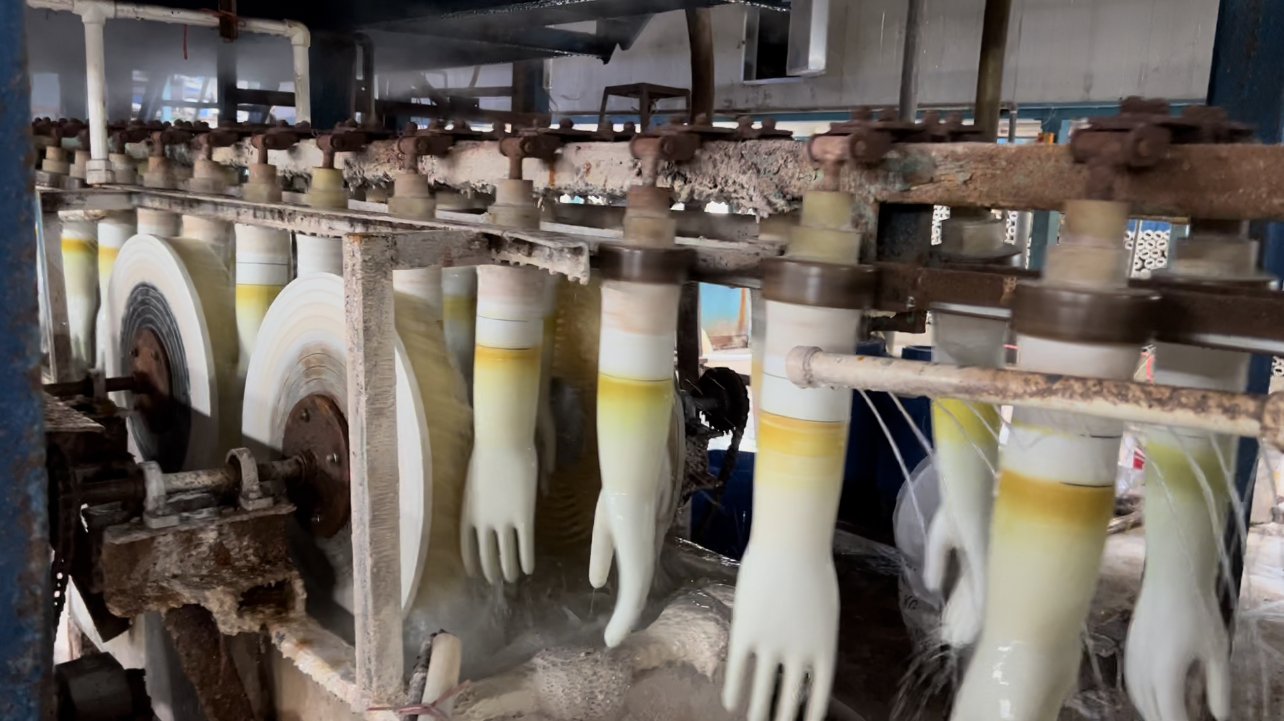

Coagulant Process
After the glove abrasive tool is cleaned, it is turned over and dried on the production line. The surface of the abrasive tool is immersed in the coagulant. Then, the abrasive tool is immersed in the material on the surface. The hand-shaped surface is made to diffuse ions into the latex combination. Through the coagulation process, the wet gel gathers. On the model, this is a very important link in glove production. The production of gloves of different weights is controlled by adjusting the coagulant.
Latex Soaking
We vulcanize the vulcanization bag for more than 24 hours, mix dozens of materials such as calcium carbonate, accelerator, color, sodium hydroxide, wheat starch, etc., stir them evenly for several hours, and then input them into the immersion pipe through a pipeline. In the cylinder tank of the abrasive tool, the abrasive tool is then put into the coating, which we usually call the batter, which is the color of the surface of the glove. It is then dried on the production line and enters the next step.


Coating Technique
Gloves are composed of two parts, one is the batter, and the other is the lining. After the batter is completed, it is turned over 360 degrees and dried on the production line, and then enters the next coating, which is what we usually call the lining. This The process is also very important. It ensures the comfort and softness of the gloves. In this production process, it is very important for us to avoid particles and impurities.
Beaded Cuff
After the gloves have completed the coating production process, they have been rotated and dried on the production line, and the gloves have been basically formed. When the gloves are still soft, we use white plastic tubes for processing. It will destroy the shape of the edge, and the shape of the curled edge is particularly perfect.


Dry Process
When the hemming is completed, the gloves will continue to roll on the production line for continuous drying, which usually takes more than 30 minutes. The production line delivers heat through steam and keeps the temperature above 110 degrees to dry the moisture on the surface and inside of the gloves. This will ensure that the gloves will not become moldy in a humid environment.
Releasing Mold
After the gloves are completed on the production line, they need to be removed from the production line. We have upgraded the production and now use automated processing. First, the gloves are blown down to the middle of the grinding tool with huge steam gas, and then the gloves are taken out with a clamp. This greatly saves labor costs and improves production efficiency. We continue to improve production efficiency, save production costs, and help customers become more competitive.
