In extremely cold working environments, it’s crucial to have appropriate protective gear to avoid injury, and one of these essential tools is thermal work gloves.
In our modern era, you have countless options for thermal gloves. However, finding a pair that suits your specific needs is paramount, but it can be challenging if you’re unsure of what you require. Here, we’ll introduce some common characteristics of thermal work gloves. Not wearing gloves in freezing conditions would be a dire and erroneous choice.
Why You Need Proper Thermal Work Gloves
Choosing suitable thermal gloves is essential for protecting your hands from cold-related injuries in extreme work environments. Frostbite, a previously unprecedented injury to the hands, results from exposure to freezing temperatures, causing tissue freezing and damage, and the severity of frostbite depends on exposure time, temperature, and individual physiology.
Similar to burns, frostbite also has four degrees of severity.
First-degree frostbite is the mildest and usually easy to treat, often referred to as frostnip. The affected skin may become red and sometimes slightly swollen, and when you experience this, warming the hands immediately is necessary to prevent further damage. By addressing first-degree frostbite promptly, you can avoid permanent hand damage.
Fourth-degree frostbite is typically the most severe, usually affecting all layers of skin and tissue, including muscles, bones, and blood vessels. The affected area may undergo complete necrosis, losing blood circulation and sensation, and may turn discolored or black, leading to tissue death, nerve damage, or even amputation.
Working in cold environments with cold tools and materials accelerates frostbite occurrence. Therefore, wearing a quality pair of winter waterproof work gloves helps keep your hands warm for extended periods, preventing injury.
Considerations When Choosing Thermal Work Gloves
Before selecting gloves, you need to understand your requirements. There’s no one-size-fits-all glove for every scenario. For those unsure of what type of gloves they need, let’s examine some common features of thermal gloves.
Insulation
This is likely your top priority when choosing thermal work gloves. If you’re working outdoors in frigid climates with temperatures dropping below zero Celsius, your gloves should typically work effectively within a range of -10°C to -30°C, and for added precaution, your gloves may need to offer more insulation than someone working in a facility at around 40°F.
You can look for insulation standards for gloves, such as the European thermal resistance standard EN511, which is for cold resistance testing. The first two tests rate the glove’s thermal insulation.
The first rating is for resistance to convective cold, insulation. It mainly tests whether the glove can resist cold air infiltration, with scores typically ranging from 1 to 4, with 1 being the lowest and 4 being the best performance.
The second rating is for resistance to “contact cold.” This rating also uses the same scoring system. Essentially, it mainly tests the performance of the gloves when grasping extremely cold objects.
Grip
Many tasks require gloves with specific grip capabilities. A strong grip ensures objects won’t slip out of the gloves, and palm coatings are a common method for increasing grip strength.
The most common types of palm coatings are polyurethane (PU) and nitrile. For general-purpose work gloves, polyurethane is often the preferred choice. Polyurethane coatings are very agile and provide strong traction. But for winter gloves, you might need to sacrifice dexterity for warmth. However, nitrile-coated gloves also offer excellent grip in wet conditions.
Therefore, you’ll often find more people opting for nitrile-coated gloves for winter gloves. Additionally, you may notice that these gloves have a sandy texture on the surface to provide even more robust grip.
Cut Resistance
If your work environment poses a risk of cuts, you’ll need a good pair of cut-resistant thermal gloves. There are two different audit standards for cut-resistant gloves, and they correspond to different countries.
ANSI 105 is the American standard for cut resistance, with protection levels ranging from the lowest A1 to the highest A9.
EN388 is the European standard for cut resistance, which contains more comprehensive content compared to the American standard. According to its standard, gloves can undergo abrasion, puncture resistance, tear resistance, impact resistance, and cut resistance testing, with corresponding ratings. Gloves tested according to this standard bear a badge with an alphanumeric code that tells you how the glove performed in each test.
Moreover, the cut levels in the EN388 standard are different from the ANSI standard. The levels range from 1 to 5, with higher levels indicating greater resistance to cuts. Correspondingly, you can choose the gloves you need based on the different cut levels.
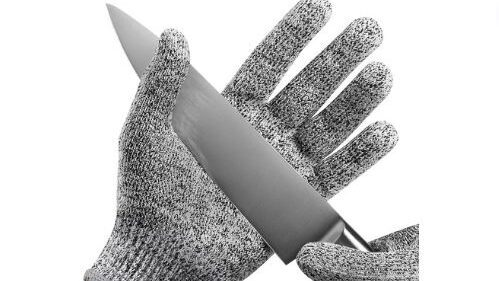
Impact Resistant
As mentioned, EN388 specifies impact levels. The United States introduced a new impact level standard in 2019 (ANSI/ISEA 138). The impact level test typically results in either pass or fail, with no grading. Gloves are either impact-resistant or not.
The impact resistance levels in ANSI/ISEA 138 are divided into three levels, with Level 1 being the lowest protection level and Level 3 being the highest. Impact-resistant gloves generally effectively reduce the impact force on the hands, preventing hand injuries caused by heavy objects falling.
Choosing the Right Gloves
Selecting the right gloves will prevent many unnecessary troubles, as ill-fitting gloves can make your work difficult. So if you’re unsure of the appropriate size, you can consult a size chart. If you’re still unsure how to determine glove size, you can contact us at Aibon, and we’ll unconditionally address any questions or concerns you may have.
How to Measure Glove Sizes – Source: AIBON
Medical Gloves – Source: FDA
Nitrile Gloves or Latex – Source: AIBON
Medical Gloves Guidance Manual – Source: FDA